Circular Economy
Circular Economy – What is a Circular Economy?
With the NCES, the German government aligns itself with the guiding principle of the "Circular Economy," as it also underpins the "EU Action Plan for the Circular Economy." The term "Circular Economy," as defined in the context of the EU Action Plan, encompasses all phases of the value chain – from product design and production to consumption, repair, waste management, and secondary raw materials that are reintegrated into the economy.
In Germany, however, the Circular Economy Act (KrWG) provides a legal definition of the term “Circular economy” that differs from the EU concept. This legal definition specifies how the term is used within the framework of the law:
"Circular economy, as defined by this law, refers to the prevention and recovery of waste" (KrWG Section 3 (19)).
Increasing circularity through the R-strategies
The NCES is built upon the 10-stage R-ladder, which ranks the core strategies of a circular economy based on their potential to enhance circularity. This approach complements the waste hierarchy established by the German Circular Economy Act.
At the top of the ladder, the R0 to R2 strategies (refuse, rethink, reduce) focus on avoidance. These strategies target:
- Consumers, including public procurement entities, by encouraging critical evaluation of their needs for products and services.
- Manufacturers, by promoting the redesign of products and services to align with circular principles in production and use.
The middle levels, R3 to R7 (reuse, repair, refurbish, remanufacture, repurpose), emphasize extending the lifespan of products or their individual components, as well as promoting more intensive usage.
Finally, the lower levels, R8 to R9 (recycle, recover), concentrate on improving recycling and other recovery processes to optimize resource efficiency.
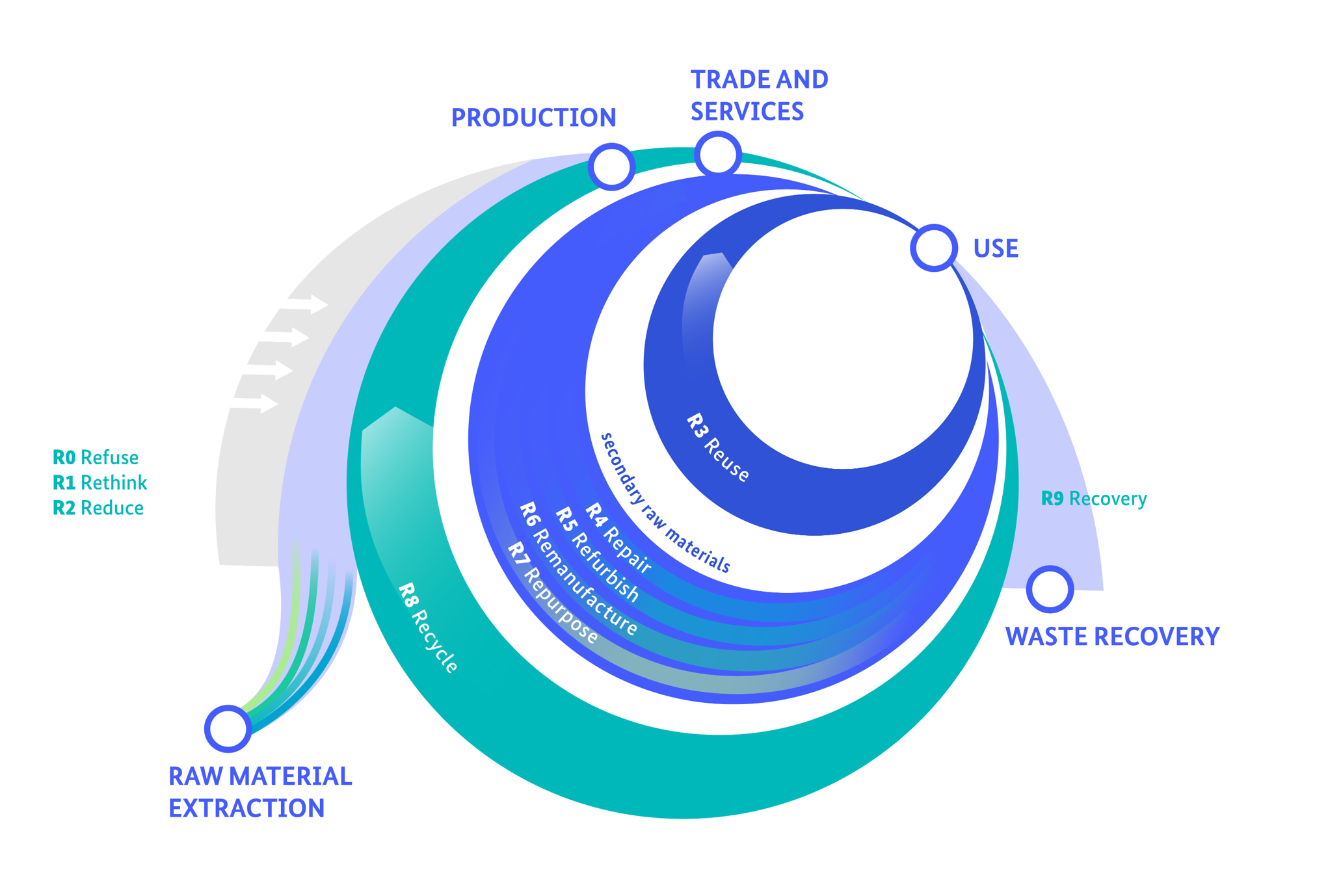
How circular economy supports climate targets:
Facts and Figures
In 2019, Germany enshrined its climate targets in the Federal Climate Protection Act (KSG), including the achievement of net greenhouse gas neutrality by 2045, as outlined in the amended version of the KSG. Achieving this ambitious goal will require more than just energy savings and the transition from fossil fuels to renewable energy in the energy, transport, industry, and building sectors. It will also necessitate an accelerated shift towards a circular and climate-friendly economy in Germany.
Globally, more than half of all greenhouse gas emissions are linked to the extraction and processing of raw materials. In Germany, the industrial sector contributes nearly 25% of total greenhouse gas emissions, with approximately 50% of these emissions stemming from the production of steel, concrete, cement, and plastics.
By systematically implementing all ten R-strategies, the circular economy holds the potential to reduce industrial greenhouse gas emissions in Germany, Europe, and globally by 30 to 50% by 2050.
Recent studies highlight that combining the circular economy with decarbonisation measures can significantly lower the costs of avoiding CO₂ emissions per tonne by 2045. This is particularly impactful in demand-intensive sectors such as buildings, vehicles, and packaging, where materials like steel, concrete, cement, and plastics are dominant.
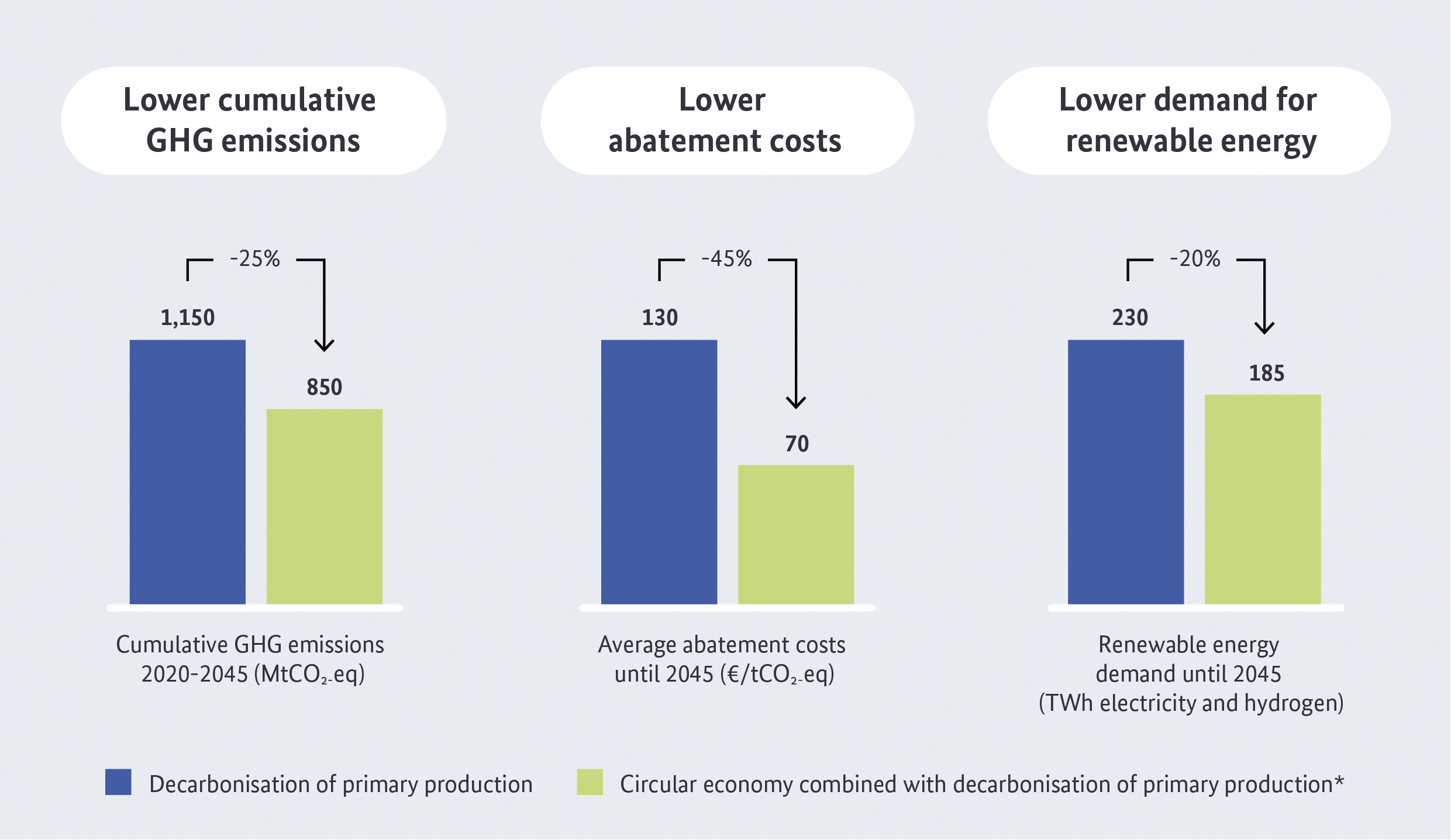
The transformation to a greenhouse gas-neutral economy can be accelerated by companies employing various strategies to promote circularity. Two examples:
- One important lever is increasing resource efficiency in production (R2), for example by minimizing material losses, adopting lightweight construction concepts in product design, or optimizing material qualities.
- High-quality recycling (R8) enables the substitution of energy-intensive primary raw materials with recycled materials, which generally cause significantly lower greenhouse gas emissions during production. The proportion of secondary raw materials in German industry is currently only about 15% overall, partly due to the frequent lack of standards and specifications for the quality of recycled materials. However, this substitution has been common practice in some sectors for many years, such as in paper and glass production, or in steel and metal production. The potential CO₂ savings per tonne of material range from up to 80% for plastics to 95% for aluminium, for example.
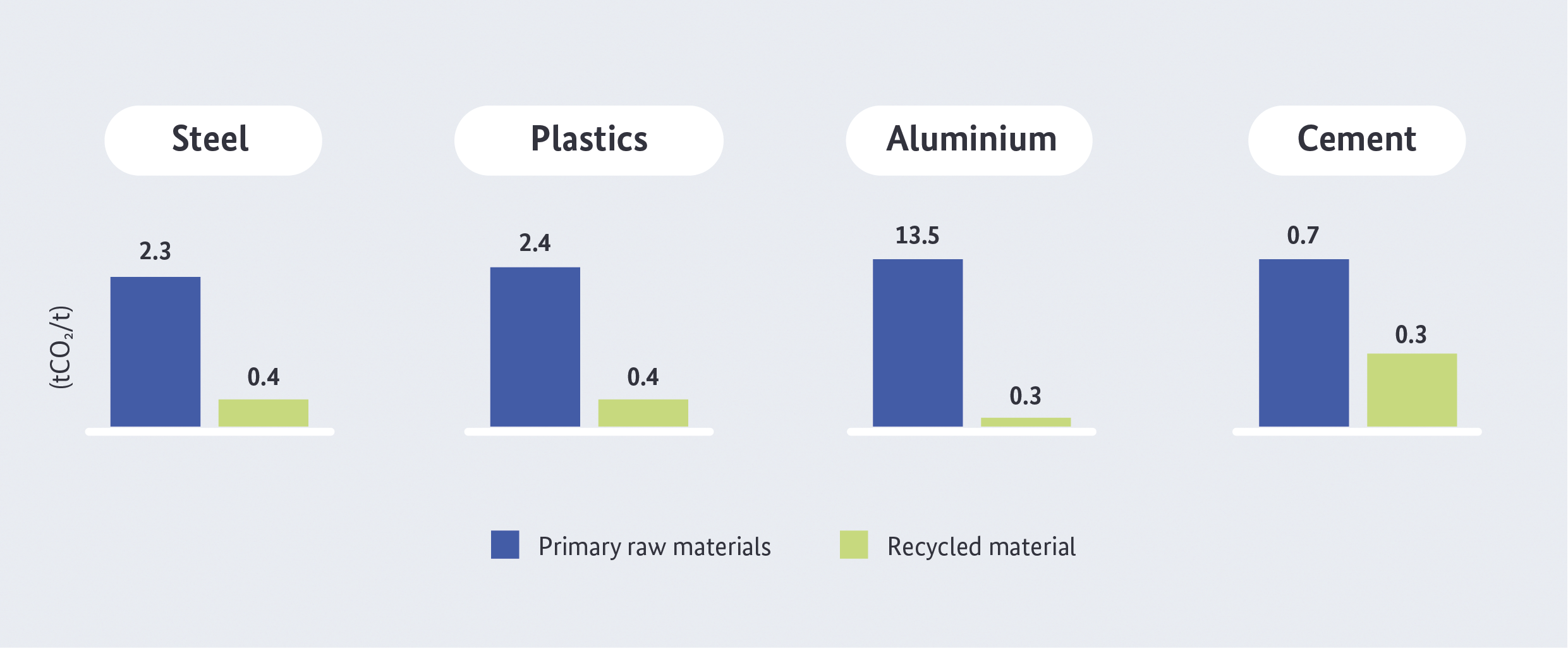